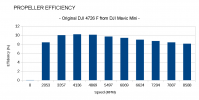
Test conditions: ESC supply voltage 8.2 V, altitude 230 m, air temperature 23 °C and air pressure 1000.2 hPa.
(Note: The measured propeller efficiency is always dependent on the efficiency of the motor and ESC used.)
The graph shows that when the propeller reaches 8588 rpm, it has an efficiency of about 8% (8.1% to be exact). However, as the rpm increases further, the efficiency drops further. These speeds produce a thrust of about 64 g and the four propellers thus produce a total thrust of 256 g. And since the weight of the drone is 249 g, at 8588 rpm it starts to climb upwards. So increasing the rpm further would not make any more sense in terms of the graph.
But the propeller efficiency of 8.1% achieved is not dazzling, creating room for significant propeller innovation. Every propeller designer should be interested in achieving the highest possible efficiency in a propeller, which will allow further modifications to significantly improve other parameters (noise, thrust, acceleration or battery life). Perhaps some propeller manufacturer (from the EU, USA, Australia, etc.) will take notice of this chart (or all the charts I have posted) and show interest in producing the first truly high efficiency propellers for the most popular drones. I can provide such a manufacturer with more of my aerodynamics knowledge to make the upgraded propellers the absolute aerodynamic cutting edge.