beanbubba
Well-Known Member
- Joined
- May 7, 2017
- Messages
- 1,845
- Reactions
- 1,408
I recharged the new battery with the charger cybernate recommended that will over pack to 4.4v.
I re-ran the identical hover test with same results except it was just shy of 40 minutes.
BTW - once voltage hit 3.0 the bird was coming down and not in a pretty fashion after about 15 seconds of up stick. Chazz might call it a hard landing
EDIT: the red alert from the factory setting to Non-DJI/4s is spot on (at least for this mod setup). Once the red alert comes up on the battery, you are running on fumes and need to find a landing spot ASAP. You have about 1 minute of controllable flight left at that point.
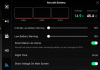
Notes taken during the flight:
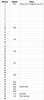
I re-ran the identical hover test with same results except it was just shy of 40 minutes.
BTW - once voltage hit 3.0 the bird was coming down and not in a pretty fashion after about 15 seconds of up stick. Chazz might call it a hard landing

EDIT: the red alert from the factory setting to Non-DJI/4s is spot on (at least for this mod setup). Once the red alert comes up on the battery, you are running on fumes and need to find a landing spot ASAP. You have about 1 minute of controllable flight left at that point.
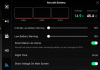
Notes taken during the flight:
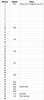
Last edited: